When your fleet starts and ends a shift at a company location, such as a warehouse, you’ll want to install charging at that location. This is called depot or “back-to-base” charging: several chargers are installed on site to serve the fleet in one centralized location. The goal is that your fleet vehicles — which can be plugged in while parked or while being loaded — are fully charged and ready to go when your employees arrive.
How to develop a depot charging plan
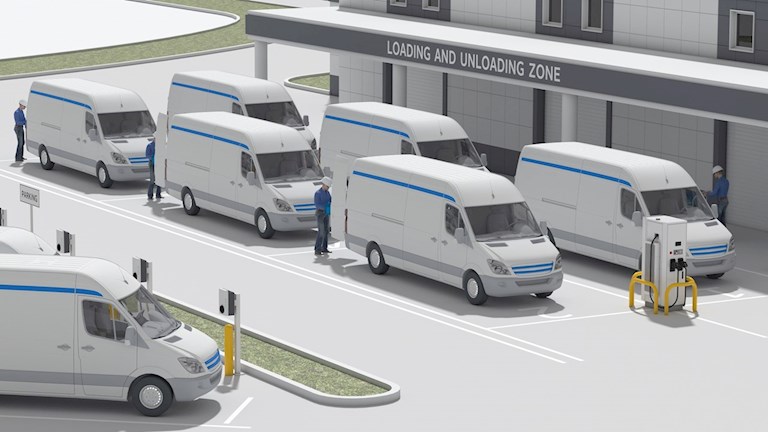
Every organization will need a different mix of charging equipment at the depot, based on their own mix of vehicles and duty cycles. Utility and fleet electrification experts strongly recommend you bring in a charging partner or consultant to guide you through the depot charging planning process. It’s also a good idea to engage your electricity utility early in your planning phases. Many utilities now offer funding for fleet electrification plans or other related support. Here, we try to simplify the steps to give you an overview of what’s involved.
These are some of the key factors that go into the plan:
- Your operations
The time the vehicles leave and return to base will determine how long they have to charge, and the power level needed to recharge them within that window. You may need a fast-charge solution for trucks that have a tighter turnaround time. - Your daily mileage
Batteries might not fully discharge if your vehicles run on routes that are much shorter than their range, meaning they only need a partial top-up each night. - The vehicles in your fleet
Each vehicle may have a different charging capability (a maximum power source that they can accept, rated in kW) and battery pack size. For instance, you might have a 7.2 kW, 9.6 kW or 11.5 kW Level 2 charger for sedans and SUVs, a 19.2 kW charger for your extended range pickup trucks, plus a DC charger if you’re operating a Class 6 truck.
It’s helpful to have a long-term view of your fleet electrification plans and an understanding of how you’ll phase in your charging plan over time, even if you don’t install all the infrastructure at once. “The best way to do planning is to begin with the end in mind: that ideally means a 10-year projection for a high-level vehicle procurement schedule,” explains Tyler Seed, business development manager at PowerOn, Ontario Power Generation’s fleet electrification consultancy.
“Even if your electrification schedule is going to change you can plan at the facility level. You don’t need to install all the chargers at once, but you want to have an idea of what the phases will look like.”
— Tyler Seed, business development manager at PowerOn
Create a parking plan
Charging can happen inside a warehouse facility or outdoors, on a lot. Outdoor locations are usually cheaper to set up, but your vehicles will be parked outside while charging, where temperature can impact charging times. Indoor depots may cost more to set up, but they protect vehicles from the weather, which makes charging more consistent.
EVs can have different charging port locations. Plan your charging spaces so that vehicles can approach them from different directions or park at different angles while still leaving plenty of space around them. Map out the locations on your facility’s floor plan, reorganize parking if needed, and determine any required electrical and construction work, such as trenching. Ideally, site the parking as close as possible to the electrical service room or transformer location.
Both standalone and wall-mounted chargers are available. Pierre Ducharme, an electrification consultant at Marcon-Miratech, recommends wall-hung dock installations whenever possible. “They cut down at least 25 per cent of the installed cost, if not 50 per cent,” he says. “You don’t need the cement base for a bollard, or a roof, or any of that. If you hang it on a wall, it’s no big deal.”
If your facility is leased, plug-in wall boxes will also be more portable if you need to move your charging infrastructure later on. And always review your lease terms before installing charging.
Share the load
Your electrician or charging consultant can help you plan your station network and charging schedule to balance the depot’s electrical load, which can help pre-empt a costly electrical service upgrade. Some advance planning to reduce load on site at peak charge times can help. “[We] try to shed load where it’s not required in order to be able to feed the trucks,” says Ducharme. “For example, if there’s air conditioning, we install a very simple device to turn it off overnight because no one remembers to do that.”
The vehicles themselves can also share networked chargers, with smart charging relaying the power to the vehicles either on a schedule or based on battery levels – with the “thirstiest” vehicles getting priority. This approach will reduce the overall power load at any given time, since all the chargers don’t operate at once or operate at a reduced kW to power-share.
Demand charges are electricity rates based on peak usage, rather than on total consumption. Originally introduced to charge factories a premium on the high volumes of peak energy they draw from the grid, demand charges usually kick in once capacity goes above 50 kW – meaning the use of a DC Fast charger once per month can trigger these higher rates.
“Lower power chargers that let you spread the load over time also help avoid demand charges,” explains InCharge Energy CTO Cliff Fietzek.
Learn more about demand charges with these articles at Electric Autonomy Canada
If your depot is unshaded and you are in a region that is blessed with plenty of sunshine, you might also consider adding solar and battery storage into your depot charging mix. The solar/storage combo is a useful tool for working around time-of-use and demand charges, since you can top up a battery with solar-generated power or with cheaper nighttime grid electricity, then use that electricity during times higher on-site demand or while primetime rates are in effect. This is also a great approach for remote and indigenous communities that may be running on diesel power.
Next up, learn more about depot charging infrastructure installation, including how and when to involve your utility in the planning process. Click Save progress to continue.
Reproduction of any or all of this material is strictly prohibited without permission. Please contact fleets@electricautonomy.ca for inquiries. Copyright © 2025 – Electric Autonomy Canada – ArcAscent Inc. – All Rights Reserved
Want to learn more? Sign up or log in so you can track your progress, earn a course certificate and receive exclusive invitations to our live learning sessions.